How a distribution center conquered mistracking and belt damage
Customer makes over USD 500,000 in annual savings and enhances overall reliability by using our tailored solution.
Just as driving a vehicle with an unbalanced load around sharp bends can easily throw you off course, bringing frustration and even danger, so a conveyor belt that keeps mistracking leads to damage, operational costs, and inefficiency. Read on to see how a customer made huge savings and improved its operational performance thanks to a better belting solution.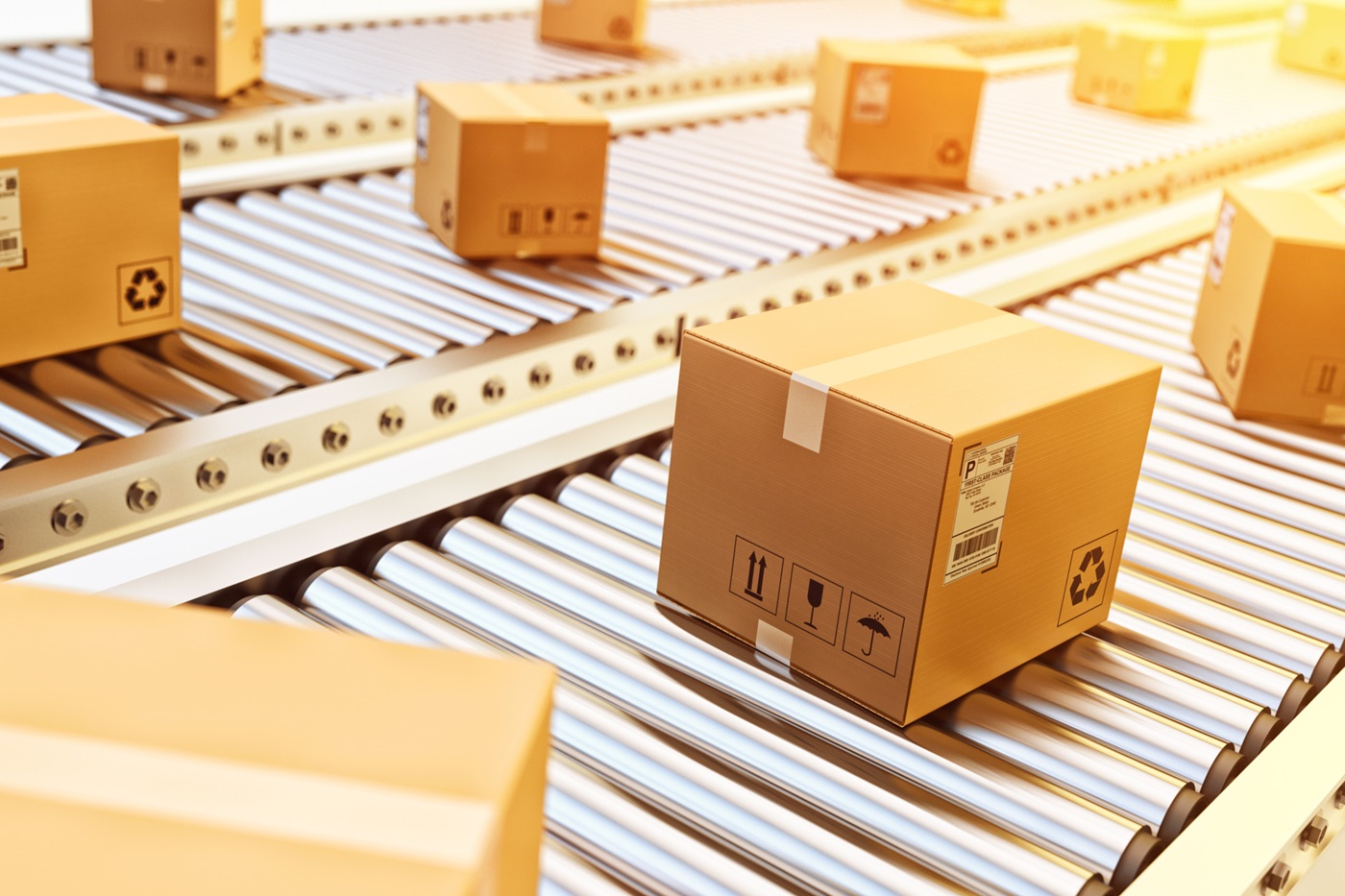
A US distribution center was moving boxes along a fast live roller conveyor, with the rollers driven by a belt underneath. Since the boxes had to be aligned with specific gaps on one side of the conveyor, the rollers were set at a slight angle, or skewed.
However, the belt driving the rollers kept going off track due to the lateral forces created by the skewed rollers. Similar to a vehicle veering off course and scraping its sides, this damaged the belt edges, which led to frequent belt replacements and downtime. The distribution center also had to buy expensive additional equipment to ensure the correct positioning of the boxes.
A bumpy ride, but the customer turned to Habasit for a tailored solution to eliminate the harmful mistracking. Working closely with the customer’s engineers to understand their requirements, it was clear they needed a replacement belt with higher lateral rigidity and different friction values on each side.
Habasit’s TMPH90MFOXB fabric belt fit the bill. While its medium friction orange peel cover firmly presses against the pressure rollers, its higher friction running side maintains contact with the underside of the roller bed, effectively preventing mistracking and edge damage. This was a game-changer for the distribution center. Not only did the solution allow the use of skewed rollers all along the line, it also eliminated the need for auxiliary positioning equipment.
The financial results were transformative: each conveyor saved $1,800 in diverting equipment, and with 300 conveyors updated, annual savings skyrocketed beyond $500,000.
Enhanced operational efficiency
In addition to these immediate cost savings on equipment, the distribution center benefited from a significant reduction in downtime for belt repairs and replacements, leading to impressively higher reliability and performance, and even enabling the execution of a previously impossible application.
Are you looking for the right support and solutions to realign your operational performance and get back on track? Contact our expert team today to help you achieve your goals and improve your bottom line.