Habasit’s Plastic Spiral Belt Delivers Annual Savings of Over $187,000
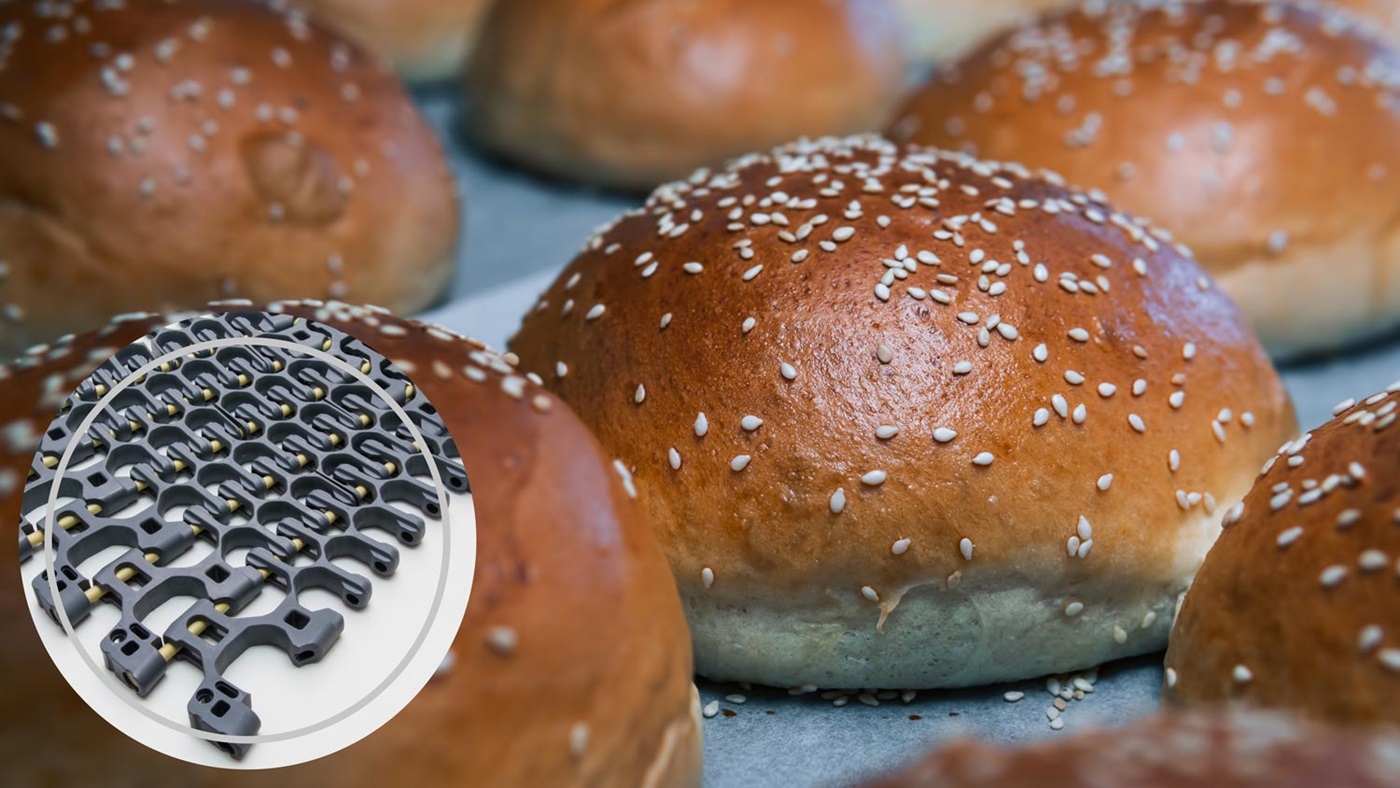
A major US bakery faced frequent breakdowns and high costs using a metal spiral cooler system to move hamburger buns to the packaging stage. Their existing metal spiral belt wore through the UHMW cage bar caps and wear strips allowing metal-on-metal contact. This led to product loss, high downtime and a severe risk of metal dust contamination.
With each breakdown costing over $100,000, they turned to Habasit’s expert spiral team for help. The bakery was looking for a reliable solution that was also flame retardant, as a fire had started at another plant where a POM (acetal) belt was used.
Habasit's solution was the HabasitLINK PR620 PA (nylon) belt, offering FDA compliance, flame retardancy (flame retardant rating UL94-V2), and reliability.
Since the retrofit was completed, the new belt has provided several outstanding benefits:
- $187,200 annualized savings (excluding manpower)
- 80% reduction in downtime (0.5 hours per week from 2.5 hours)
- Enhanced service life thanks to decreased wear on UHMW components
- Quick and easy module replacement with Habasit's rod system, no metalwork
- Efficient cleaning and maintenance, eliminating metal or black residue contamination
- Energy savings from reduced chain pull
With zero belt failures since installation and significant savings, the bakery retrofitted two additional belts. Habasit provides a comprehensive range of products for spiral cooling, proofing, and freezing systems, including flame-retardant PA and PA+FRF options for safety.
Contact us today concerning your specific needs.